The automated fabric inspection systems by USTER® are designed to offer a bouquet of benefits to its discerning customers – from reducing wastage to improving yields.
USTER® fabric inspection solutions cover the industrial value chain from weaving to finishing. The company’s U-BAR 2 and EVS FABRIQ VISION is suitable for all production lines – be it delivering quality or optimizing fabric yield.
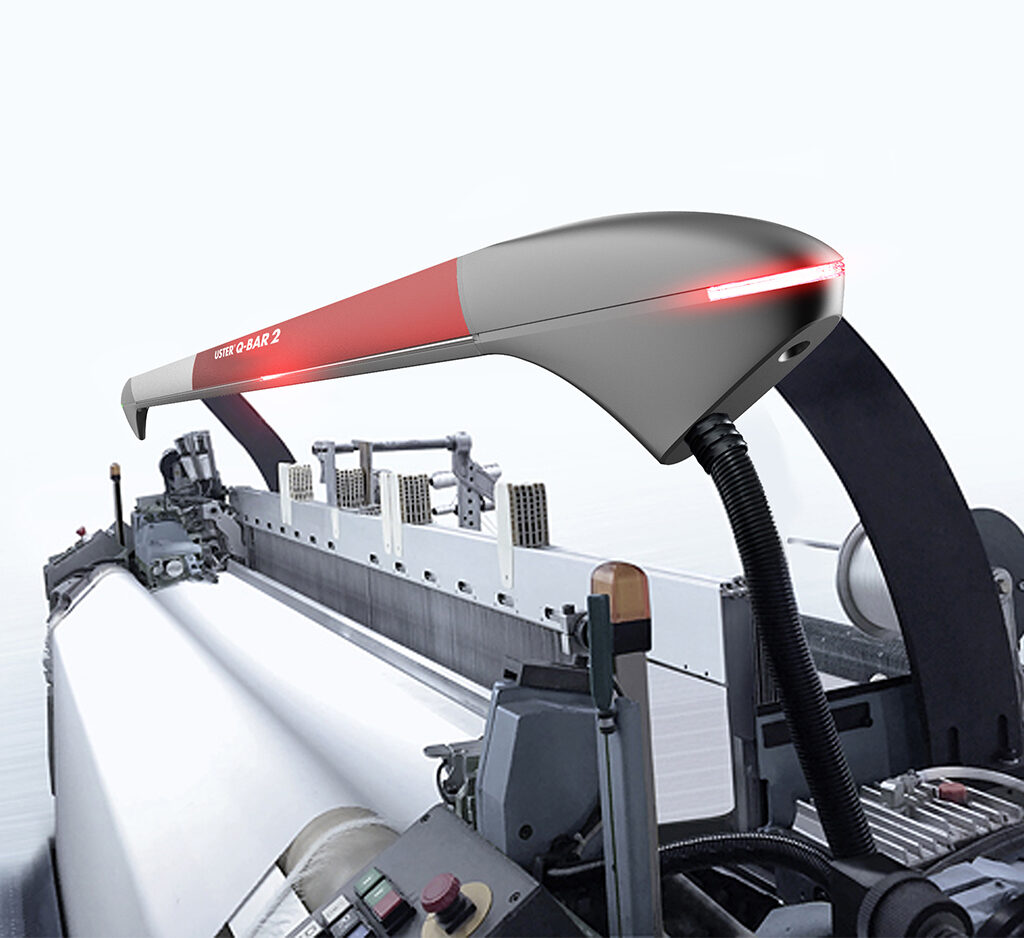
The solutions fulfill the requirements of the technical textiles especially those of quality and precision. Industries such as automotive, applications such as airbags, headliners, upholstery and tire cords need zero defect quality standards to be met with.
USTER® Q-BAR 2
USTER® Q-BAR 2 is a fabric quality monitoring system that prevents waste. Its slim design allows for a simple installation process on existing weaving machines. It is part of the latest generation of on-loom monitoring and inspection systems and offers operation improvements to weavers. Its placement on the machine allows for earliest detection of fabric defects, thus reducing downtime of the operations and minimizing material wastage.
Additionally, USTER® Q-BAR 2 creates a ‘defect map’ for each roll which can be reviewed at a later point in time. The system allows classification possibilities according to number, size and position of defects and customer criteria. It reduces the need for post-weaving inspection for most applications.
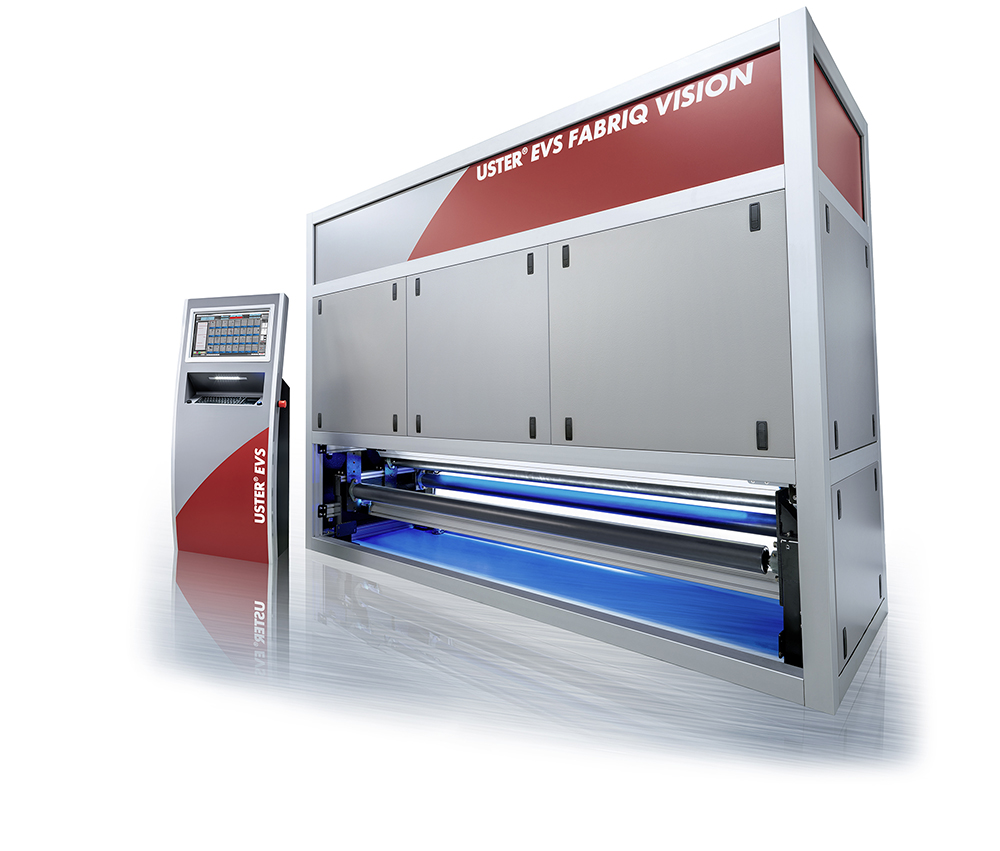
USTER® EVS FABRIQ VISION
USTER® EVS FABRIQ VISION is a fabric quality assurance system that ensures first-quality yield for all applications. It has a high rate defect detection and offers optimized efficiency in grading by using automated control during intermediate and final inspection. By creating a roll inspection chart, the system eliminates laborious manual inspection saving on cost and resources.
USTER® EVS FABRIQ VISION’s cut optimization software module works on fabric yield per class. Infrared ink is applied on the fabric during the inspection process and defect positions are synchronized with the cut optimization software module. The infrared ink guides the inspection table to stop precisely at each defect with minimized errors.
Both the systems have become the benchmarks in quality standards with efficient control over fabric defects around the world.