Trützschler Nonwovens & Man-Made Fibers GmbH started a cooperation with the Italian textile machinery manufacturer Texnology S.r.l. in the field of needle-punching technology. With immediate effect, the companies will offer complete production lines for needle-punched nonwovens under the name of T-SUPREMA.
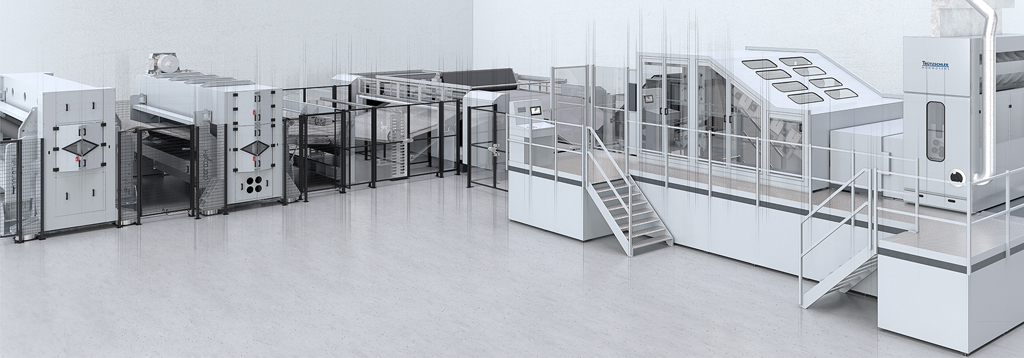
Web bonding with steel needles represent the largest production process in the drylaid nonwovens segment. The areas of application are predominantly of a technical nature, with the largest applications being durable geotextiles, automotive textiles and filter media. The high adaptability of the needling and finishing processes as well as the broad material base result in a large number of different end products. Needle-punching is suitable for a wide range of man-made and natural fibers including mineral and high-performance fibers.
Trützschler Nonwovens contributes its many years of experience in fiber preparation and web forming to the cooperation. Texnology is mainly responsible for the needle-punching process. Joint projects can thus build on a broad application expertise.
“With Texnology, we have an innovative and reliable partner at our side. The company already sets an important course in the field of needle-punching machines through excellent and patented solutions,” says Klaus Wolf, Managing Director of Trützschler Nonwovens. “Trützschler Nonwovens is returning to needle-punching solutions. In the partnership, we are able to serve this interesting market segment with precisely fitting production lines. With T-SUPREMA needle-punching becomes as easy as never before.”
Nicola and Paolo Olivo, owners of Texnology S.r.l., also see the joint activities as an opportunity: “Texnology has developed its own needling technology with patents and profound know-how. Collaborating with a well-known, globalized company like Trützschler Nonwovens will significantly increase our target group.”
A first joint project has already been successfully completed, implemented and put into operation.