Marco Fano CMO AUTEFA Solutions:” We see that the spunlace sector is still challenging for product manufacturers. AUTEFA Solutions offers complete lines for the production of direct and crosslapped spunlace products. The web forming process, consisting of the Injection Card and Crosslapper Topliner CL 4006 CL, is the key for high and consistent nonwoven fabric quality. The crosslapper of the Topliner series, combined with WebMax and CLOSED LOOP system prevents the increased weight of the fabric in the edge areas, called the smile effect. This results in an excellent uniformity in the fabric and, thanks to a considerable saving of materials, a reduction in material costs. AUTEFA Solutions advanced Spunlace technology with Hydroentanglement Machine V- Jet Futura and Square Drum Dryer SQV offers a quick return on investments.”
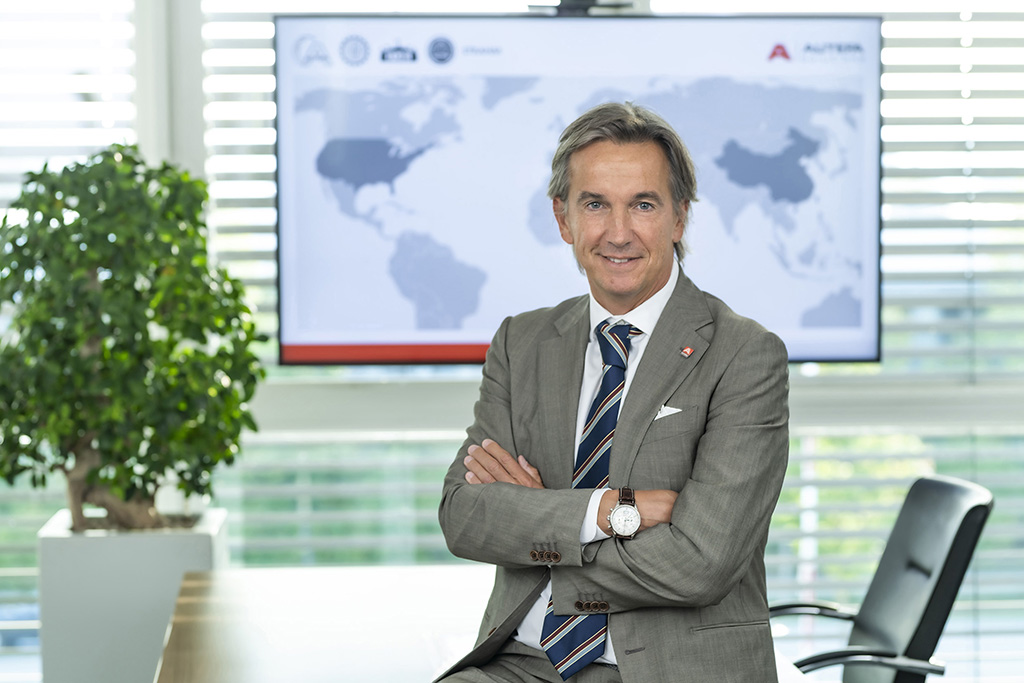
As a customer-oriented company, it is AUTEFA Solutions continuous obligation to offer new ways how to increase productivity, improve quality and at the same time reduce energy consumption as much as possible. All of these energy efficient technologies were recently introduced to the market. AUTEFA Solutions has reached the goal to achieve even better performance with less energy – which is especially important in the hygiene industry, where energy and raw material represents a big share of manufacturing costs. The company sees a strong market request for biodegradable products as well as for spunbond, wetlaid or crosslapped drylaid, increasing the large range of spunlace applications.
The demand for sustainable nonwovens is clear and a leading topic in most discussions with customers in all fields of spunlaced Nonwovens. Even in the area of Geotextile and clothing sustainability of spunlaced products is becoming more and more important. The fact that spunlaced products can be made with up to 30% less energy consumption, compared to existing traditional spunlace technologies is opening up new markets, even in high fashion products like artificial leather based on natural leather waste and other sustainable products. AUTEFA Solutions offers machines and lines for more sustainable manufacturing. With the energy and raw material saving solutions, AUTEFA Solutions contributes to the increasing importance of resource saving.

Energy costs is the one of the biggest shares in the conversion cost of Spunlace products. The V- Jet Injector enables customers to modernize existing production lines with the latest AUTEFA Solutions hydroentanglement technology. With the patented V-Jet, AUTEFA Solutions has introduced a pioneering new development in energy transfer as compared to other systems on the market. The geometry of the nozzle bar and the nozzle strips in the V-jet and the distance between the nozzle strip and the underside of the nozzle bar is reduced from 25-40 mm to 10 mm. This reduction in distance between the nozzle outlet and the nonwoven surface means that negative influences such as energy losses due to air friction, air turbulence and jet expansion over the free jet length can be reduced to a minimum. This facilitates increased nonwoven bonding at the same water pressure or energy savings through reduced pressure with the same strength of the spunlaced nonwoven fabric.
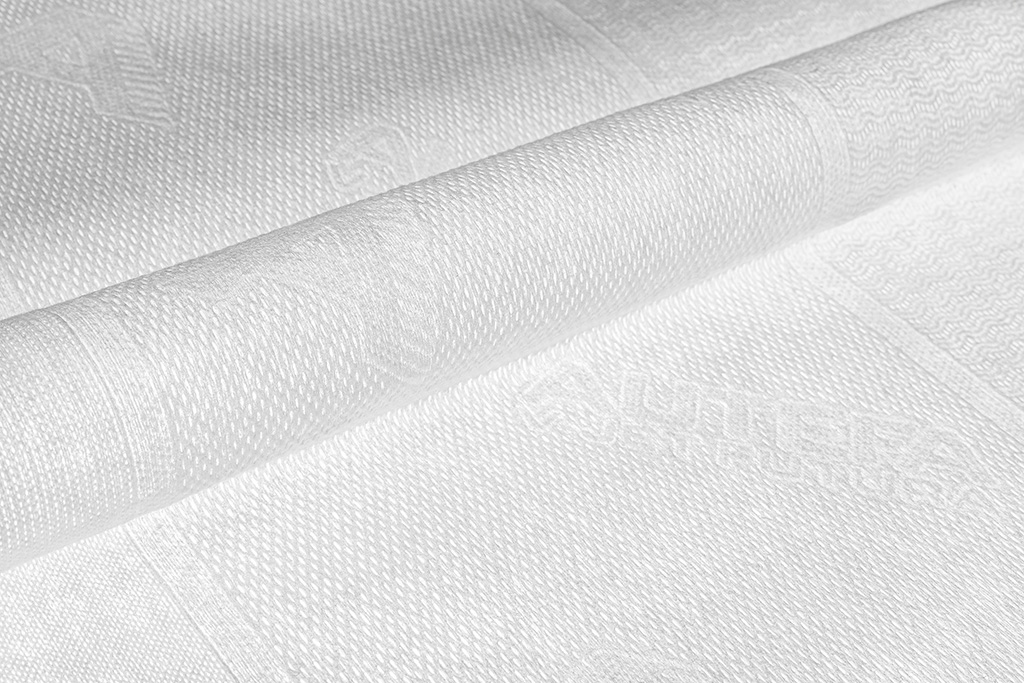
The fact that spunlaced products can be made with up to 30% less energy consumption, compared to traditional spunlace technologies, is opening up new markets as reduced cost of manufacturing leads to advantages in the ever-competitive marketplace.
General: Behind the name AUTEFA Solutions are companies that have a long tradition and many successful years on the market. These include the companies AUTEFA in Friedberg (Bavaria, Germany), Fehrer in Linz, Austria, FOR and OCTIR in Biella, Italy and Strahm Hi-Tex in Switzerland. The individual companies AUTEFA Solutions Germany, AUTEFA Solutions Austria, AUTEFA Solutions Italy and AUTEFA Solutions North America were founded in 2011. These were followed by AUTEFA Solutions Switzerland and AUTEFA Solutions Wuxi.