Outstanding meltblown and spunbond technol-ogy for the production of synthetic filter media
“We love building systems, machines and components that sustainably manufacture the materials your successful products are made of”, promises Dr. Ingo Mählmann, Head of Sales at Oerlikon Nonwoven. This claim expresses the company’s passion for continually improving its technology and the strong partnerships with its customers. Oer-likon Nonwoven is now – for the very first time – exhibiting at the leading trade fair for filter and filtration systems – the FILTECH in Cologne, Germany (March 8-10, 2022). The Neumünster-based manufacturer of nonwoven systems and equipment will be taking the opportunity to focus on market- and customer-oriented system solutions for filtration applications. Trade fair visitors will be able to meet the team and delve into the company’s comprehensive product and process know-how at trade fair stand B18 in Hall 8.
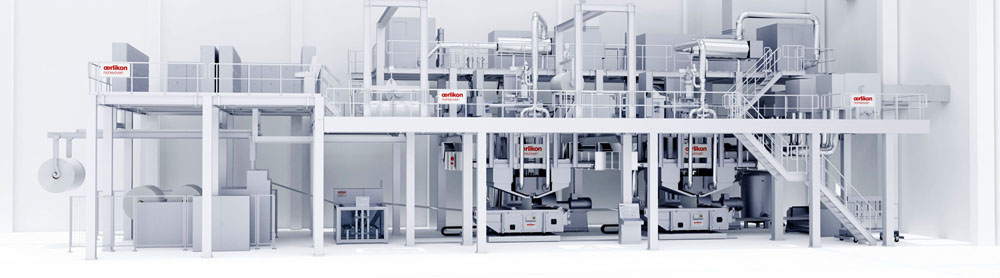
Filtration: leading meltblown competences from Neumünster
Unique and highly-sophisticated nonwovens for filtration, insulation and sorption applications can be simply and efficiently manufactured thanks to Oerlikon Nonwoven’s meltblown technology. The poly-mers used to produce the filter media and membranes are as diverse as their field of applications. The spectrum ranges from classical polyolefins (PP, PE), PET, PLA, PBT and PA all the way through to special plastics such as PPS and TPU. All these, and other raw materials, can be reliably processed using the Oerlikon Nonwoven meltblown technology.
Filter media can be efficiently electrostatically charged with the ecuTEC+ electro-charging unit devel-oped by Oerlikon Nonwoven for increasing the filtration performance of meltblown media without reduc-ing air permeability. It distinguishes itself from other concepts currently available on the market as a result of its extreme flexibility. Users can choose from numerous possible variations and hence set the optimum charge intensity for their respective filter applications. However, ecuTEC only represents the beginning of an era of new charging and treatment systems available from Oerlikon Nonwoven for fur-ther increasing media filtration performance and product diversity. Trade visitors are invited to visit the Oerlikon Nonwoven stand to take a closer look at this brand-new product and its unexpected perfor-mance possibilities.
High-performance technology for industrial nonwovens – Spunbond solutions for filter applica-tions
Oerlikon Nonwoven systems for industrial nonwovens are capable of high production capacities and yields with simultaneously low energy consumption. In addition, spunbond products are also becoming increasingly important in filtration applications – both as backing materials for filter media and as the filter media itself. An engineered nonwoven structure permits the inclusion and/or combination of differ-ent customer-specific requirements for various functions into just one layer. It is Oerlikon Nonwoven’s many years of bi-component spinning experience in particular that enable the creation of completely new nonwoven structures and hence the incorporation of various functions in a single material. The bi-component spinning process allows the combination of various fiber cross-sections and simultaneously the manufacture of different fibers from a single or different polymers using only one system. The spec-trum ranges from classical core-sheath and side-by-side bi-component filaments, splitable fibers all the way through to so-called mixed fibers.
3,660 characters including spaces