Lubrication is rarely a topic that textile manufacturers put into focus. Yet, there are many lubricants in use for spinning, knitting, weaving, and finishing. Needle and sinker oils are the most used lubricants on circular knitting machines for example. Further, compressor oils, hydraulic oils, chain oils, bearing greases and multi-purpose lubricants are needed to reliably operate the machines in the textile industry.

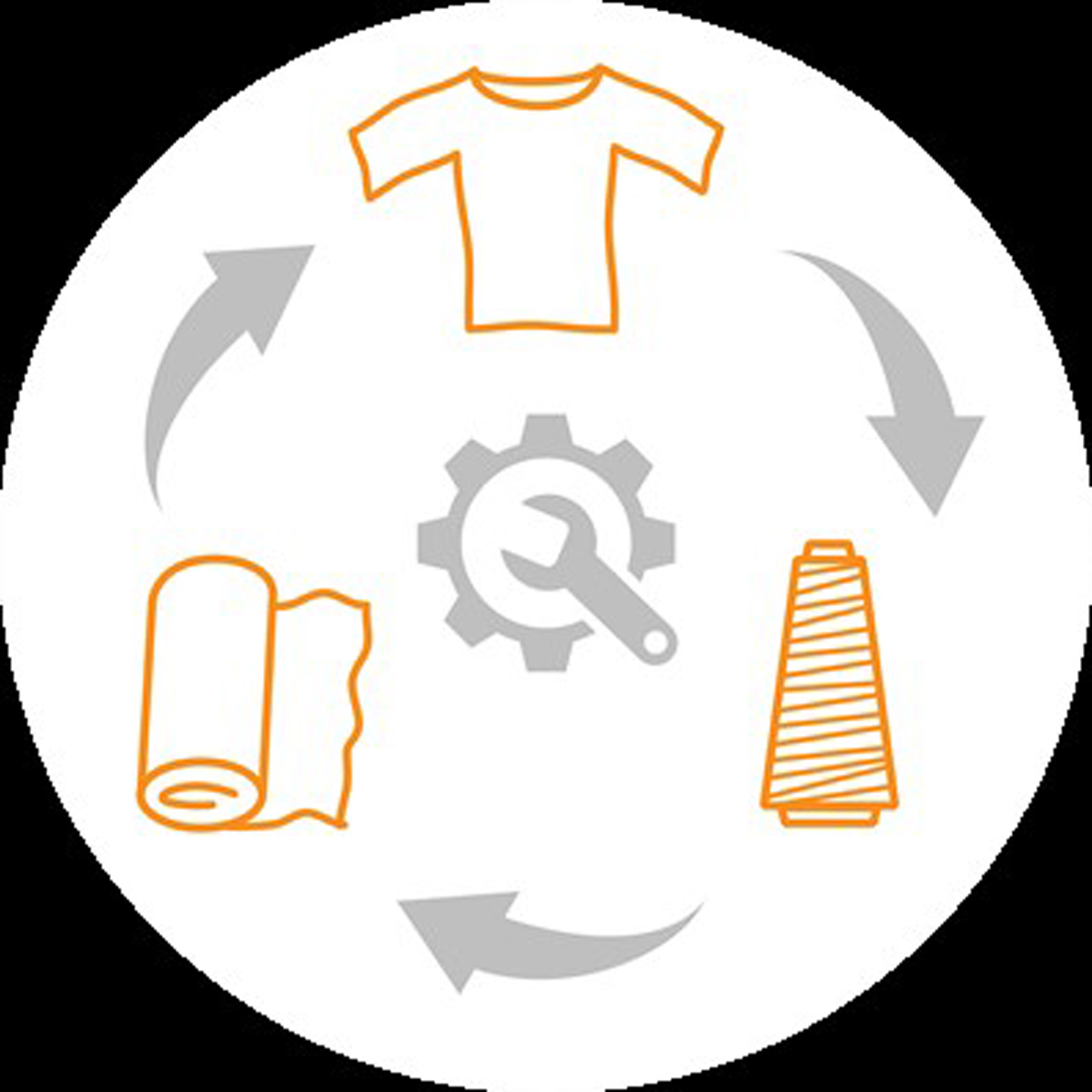
The impact of special lubricants
Considering the impact that lubricants have on your productivity is smart, since special lubricants are available that reduce the energy input by a low coefficient of friction and guarantee a long service life of the moving components, and therefore ensure a resource-conscious and competitive production. This directly affects your carbon footprint. Moreover, a closer look at the small cost factor of lubricants does influence the productivity.
Well-balanced special lubricants
What does make a lubricant special and thus has the potential to positively affect the productivity? Special lubricants are thoroughly tested in the laboratory on its characteristics that are important for its later application. This procedure results in a very well-balanced formulation at the end of the development for the finished product.
Needle and sinker oils according to DIN 62136
Regarding needle and sinker oils the challenges for the lubricant are vibrations, friction, and diverse material compatibility issues also with electronics. Further, the lubricant should not stain the valuable fabrics or at least it should wash out easily with common detergents.
The well-balanced formulation of the FLUID-setral-KN … N series with clear oils and additives results in a colorless, scourable, anti-wear needle and sinker oil. The lubricant series is tested according to DIN 62136-1:2014-03 and is available in ISO VG 22, 32 and 46. A low coefficient of friction allows ideal energy intake without sacrificing wear protection. They performed excellently in wear and coefficient of friction in the tribology test with the translatory oscillating test rig (SRV). The washability has been confirmed by Groz-Beckert® a well-known manufacturer for needles.

The skillful combination of the base oils reduces deposits that could lead to clogging of the needle channels, for example. Therefore, a minimization of the maintenance effort and thus the maintenance costs – also because of the high wear protection – is quite possible. The electrically insulating character of the FLUID-setral-KN … N series means that a good compatibility with electrical components can be expected. These special lubricants are tested on a low corrosion effect on copper and steel.
Other lubrication points
Depending on what part of the textile industry you represent other lubrication points are of interest for a reliable and resource-conscious production. For the finishing of textiles in stenter frames it is significant to use a high-temperature chain oil in the drying oven. Regarding greased bearings either a multi-purpose grease is sufficient or at extreme temperatures a special high-temperature grease is required.
Generally, an excellent gear oil, compressor oil and hydraulic oil on synthetic basis supports the productivity by long oil change intervals supports, less maintenance time and waste oil and, of course, a reliable performance.
Discover the setral® product portfolio with special lubricants for the textile industry. Besides the above mentioned it also includes bonded coatings, pastes, fine oils, corrosion protection and more. Comprehensive consultation is always the focus at setral® before the use of special lubricants. Operating in more than 80 countries, setral® lubricants are available on site. The company setral® is certified climate positive. For the best efficiency of your textile machine with reduced energy input, low carbon footprint, long equipment lifetime, less downtime and/or extended relubrication intervals, contact the lubricant experts or meet us from June 8th – 14th in hall 18 B booth 104 at the ITMA in Milan, Italy.