Significant savings in energy consumption can be achieved by finishers through the use of innovative heating technologies from Santex. The ingenious heating and drying systems in Santaframe, Santashrink and Santasynpact machines deliver sustainable production with low CO₂ values – along with notable cost savings. The three also share the benefits of great performance in productivity and finishing quality.
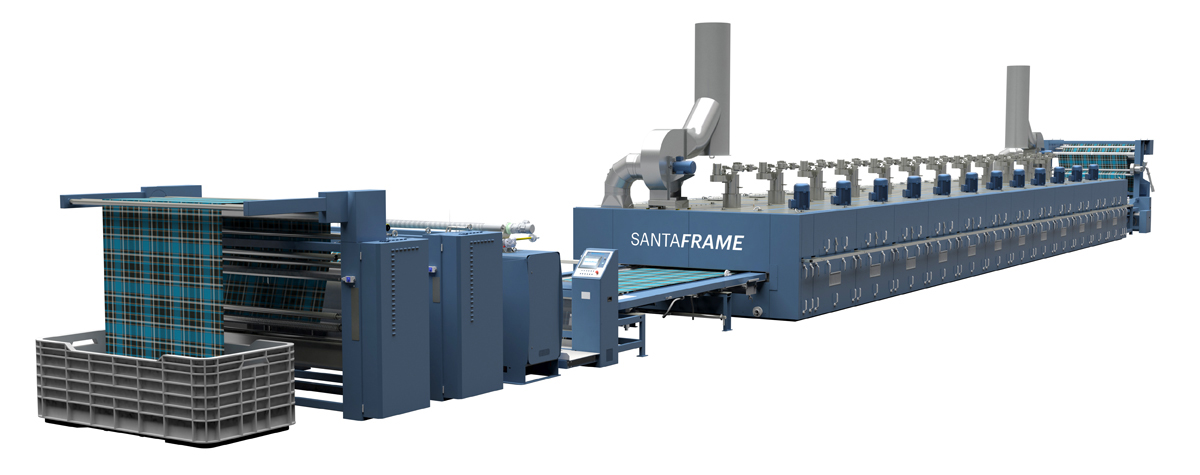
Santex Rimar has been synonymous with technological excellence since 1982. A member of the multinational Santex Rimar Group, the Swiss company has a clear focus on saving water and energy as part of its commitment to sustainability. This philosophy also leads to reduced production costs for its customers, by promoting cost-efficient manufacturing with no compromise on the quality of finishing results. This article presents the evidence!
Air-flow technique is key
Santaframe is a high-performance stenter for top-quality processing of knitted and woven fabrics. Energy-saving innovations drive customers to sustainable production with low CO₂ values. Unmatched low energy consumption is based on a new and unique air-flow technique with the Aero-Surf nozzle system. By directly using residual heat from exhaust air, the system saves even more energy.
Conventional energy-saving units use hot exhaust air to preheat the incoming fresh air via external heat exchangers. But the Santex Energy Saving Chamber (ESC) applies hot exhaust air directly to preheat the incoming moist fabric. Efficient use of energy is ensured by the air exchange in the ESC – proven by the reduced exhaust air temperatures at the exit point.
Installing Santex ESC ahead of Santaframe heating chambers results in energy savings of up to 25% by optimal use of residual heat from the exhaust air, fed into the ESC. As a result, the fabric is preheated without the need for extra heating power. The concept of using the material itself as a heat recovery medium is possible only through the unique solution for evenly distributed heating air and the exhaust air ducting integrated into the heating chamber.
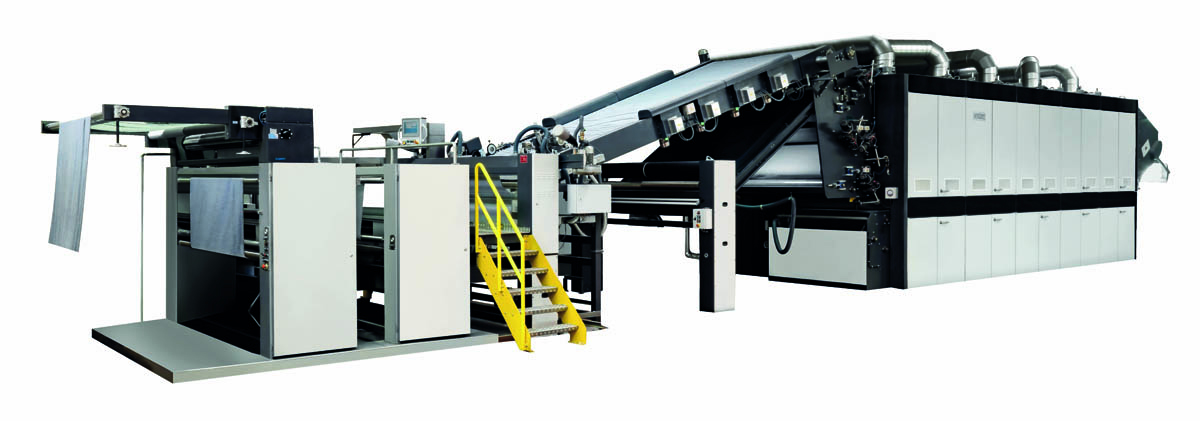
In fact the ESC boosts productivity in finishing by up to 20% and the resultant fabric displays softer handle and better shrinkage values. This arises from the Santaframe air-flow technique, in which the fabric is conveyed on a cushion of air.
Two heat recovery systems
The Santashrink machine is applied for shrinkage, relaxation and tensionless drying of tubular or open-width knitted fabrics. Combined with the ESC or Enairsave system, the drying process operates with significantly better energy savings – making Santashrink the most optimized drying process for sustainable textile finishing.
The use of two heat recovery systems has clear advantages. ESC reuses energy directly, while Enairsave works indirectly. By optimal use of residual heat from the exhaust air fed into the ESC, the fabric is preheated without extra heat energy needed, as with the Santaframe. Adding the ESC to a new or existing Santashrink lifts production capacity by up to 25% with the same input heating energy.
The Enairsave heat recovery unit is installed on the dryer exhaust duct. This system is based on an air-to-air heat exchanger, using a rotating heat-absorbing component. The rotating system, divided into two sections, is heated by exhaust air from the dryer and it then preheats incoming fresh air returning to the dryer. In this way, the energy consumption of the dryer is reduced by 20%.
The Santashrink series for tensionless drying is available in three versions to meet the requirements of drying capacity, available space and quality demands. These are the standard (single passage dryer), the jumbo version (double passage) and the super jumbo version (triple passage).

These Santashrink versions are the basis for the Santashrink Progress machine, specifically for open-width fabrics, which is usually equipped with three or more drying chambers and highly efficient padders. The technical and economical design of Santashrink Progress gives several application advantages for open-width fabrics, reflected in the excellent residual shrinkage results. These benefits make Santashrink the most requested dryer on the market.
Steam control in flexible width
Santacompact RD and Santasynpact are established as levelling, steaming and compacting calenders with extremely gentle fabric handling. Both the Santacompact RD open-width felt belt compactor and the Santasynpact sanforizer feature a high-performance V-steam box, which is connected to the guide rail to avoid steam distribution outside the fabric web. This results in a far more controlled process, and a 50% reduction in energy compared to conventional steam tables. Furthermore, the V-shaped steam box adapts to different fabric widths – and it is reported that Santex compacting machines provide the best dimensional stability for the finishing of high-quality open-width knitted fabrics.
Santex Rimar recently launched the 3-zone felt belt compacting machine Santacompact RD Plus. The Plus denotes an additional larger compacting zone at the exit for open-width fabrics. This extra compacting zone achieves excellent residual shrinkage values, especially for structured fabrics such as Pique, Lacoste, Waffle, etc.. This is achieved in only one pass at high productivity rates, without smoothing the fabric structure. The machine can even process sensitive knits at speeds of 40 m/min or more.