Haren Textiles Private Limited is an ideal example of where a traditional mill evolves into a future-ready textile mill towards achieving Industry 4.0 through digital technology, real-time tracking and seamless management information system through ERP
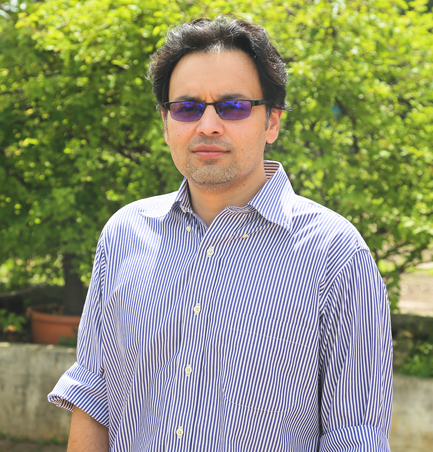
A 57-year-old company with actually a history of 81 years, Haren Textiles (P) Limited was started in 1964 by Krishna Kumar Mehta for making fabrics that are now labelled as technical textiles. At the time it was made, no classification existed. The fabrics were known by the performance criterion, the functions it had to meet and the way it was manufactured. This was then an emerging sector with fewer buyers and fewer manufacturers. Those decades were full of fashion fabrics, constantly changing fashion, and very long production runs of a few commoditised fabrics.
As another group mill, The Ambika Silk Mills Ltd., was already making such fabrics since 1954, Mehta commenced a new mill in 1964, christened it Haren Textiles after his oldest son, and mandated that this new fully integrated mill would always make specialty fabrics of the time, invest as much as needed for the time, and plough back what it earned. This continues even today. His vision remains strictly in place today just as it was 57 years ago to maintain a sustainably stable business of technically specified fabrics with newest machines as needed for today and for the future.
Led by Technology
Haren Textiles has witnessed evolutions after technological revolutions and breakthroughs. It is presently managed by the third generation of the family and they continue with constant upgrades of both technology and products. The company’s archives hold interesting anecdotes. For example, Haren Textiles was amongst the first warp knitters. When K Liebrandt, owner of Germany’s LIBA Maschinenfabrik, now owned by Karl Mayer Gmbh, himself came to sell and then sent German technicians to install their machines, teach the personnel and ensure that this new fabric forming technique would spawn a generation, Haren Textiles sent its technical team to Germany to work at their plant for many months.
Haren Textiles was also amongst the first to get water jet weaving machines at Ambika Silk Mills in 1969 from Tsudakoma, Japan through the then Nissho Iwai Corporation, Japan, which soon became a benchmark for others. K M Mehta, recognising the potential, had ingrained his vision of establishing Haren Textiles as a quiet, stable and investment-enthusiastic company to produce specialty, customised and technically advanced textile which was ethically made to customer specifications. Then and now, this ethos continues. Haren Textiles continues to be regarded as a formidable competitor and a respected mill in the Indian textile industry.
The vision has always been to transform people’s lives through innovation in textiles. Through the years it continues to live up to expectations of everyone associated with it. Today, it is managed by its Director Nishant Mehta. “Haren Textiles has grown significantly over the years. It is recognised as amongst the good specialty fabric-maker in the country. The company continues to operate its fully integrated textile mill with globally sourced automated ERP-linked manufacturing machines for 100% synthetic fabrics, Polyester, Nylon 6 and Nylon 66,” he informs. One of the company’s numerous unique selling propositions is that the entire fabric it produces from weaving to finished dyed and coated fabric is entirely manufactured in-house in its own mills. It will only sell what it produces.
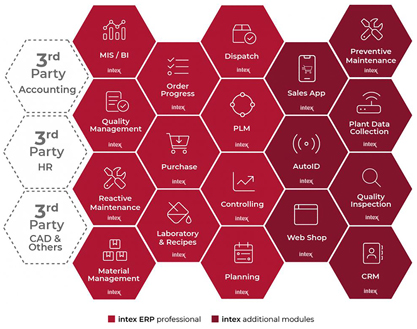
Haren Textiles continues to use newer, faster and more energy-efficient German warp knitting and Japanese water jet weaving technologies. Moving towards carbon-neutral, using solar and alternative fuels and being fully compliant with environmental norms, the company remains committed to responsible manufacturing. Its fabrics are found in garments, made-ups and accessories of large brands in the US, Western Europe and mail order catalogues. The fabrics are used in athletic sportswear, outdoor wear, footwear, medical PPE, and military and customer specified end uses.
Perfection with ERP
With proximity and access to the port, Haren Textiles’ customers benefit from just in time (JIT), flexible manufacturing and short lead times. With its ITS-accredited quality assurance laboratory where all fabrics are fully tested before, during and after production, the need for tracking fabric from yarn to the final finished fabric as it flows through its mill becomes important. With instant information, repeatable standard operating procedures, guaranteeing the same shade each time, guaranteeing that the fabric made is in compliance to a customer’s order, Haren Textile’s purchase of Intex ERP remains an integral part of its success.
The company has achieved many certifications. It is CE-certified, FDA-certified, ISO 9000, ISO 14000 and ISO 13485-certified for medical textiles, ISO 14000-certified for environment management and SA8000-certified for social accountability as well as Oekotex100 and GRS-certified for its recycled polyester and nylon fabrics. In fact, Haren Textiles was announced among the top ten most admired textile mills in its class. With its long-standing supplier relationships and longer standing customer relationship with leading global and domestic brands, Haren Textiles places great emphasis on its people and continues to be a responsible, sustainable and fully environmentally compliant textile mill adhering to global standards and benchmarks.
The long-standing association shared by Haren Textiles and Intex demonstrates system-wide efficiency that uncovers hidden waste and reworks in full safety and security. The operation of machines and SOP systems is critical in determining the quality of the fabric produced. Haren Textiles remains a loyal customer to Intex Consulting. As Nishant Mehta says, “We can now track and trace our products in real-time with significant reduction in labour time and effort and with greater accuracy in reliable verifiable data. Internal certainty at a time of external uncertainty is a huge benefit for us and our consumers.” Mehta adds that after initial months of hiccups and system formalisation along with training and customisation, Intex ERP has shown a stable performance and provides reliable post-implementation support. Intex Consulting offers a comprehensive ERP package, including frequent upgrades, customisations and quick post-implementation support. As such, the cooperative association between Intex Consulting and Haren Textile has proven to be successful with long-lasting benefits for both. A recent survey has shown that customers continue to choose Haren Textiles as their preferred supplier over many others. Mehta credits the company’s success to the relentless striving multitude of dedicated, hardworking and responsibility-conscious team members across its mills.